Entgraten von Metallbauteilen
Entgraten auf einen Blick
Entgraten von Metall – für funktionale und sichere Bauteile
Geht es um die Sicherstellung der Funktionalität von Bauteilen und Maschinenelementen, ist das Entgraten von Metall ein unerlässlicher Bearbeitungsschritt. Aber auch die Minimierung von Verletzungsgefahren spielt hierbei eine entscheidende Rolle. Je nach Werkstoff, Form und Verwendungszweck der hergestellten Metallbauteile sind unterschiedliche Methoden geeignet, um Metallgrat prozesssicher zu entfernen.
Für das Entgraten von Metall verfügt plasmotion über innovative Technologien auf Basis unserer einzigartigen plasmaelektrolytischen Abtragswirkung. Hiermit gelingt es uns, Metallbauteile schnell, hocheffizient und nachhaltig zu bearbeiten.
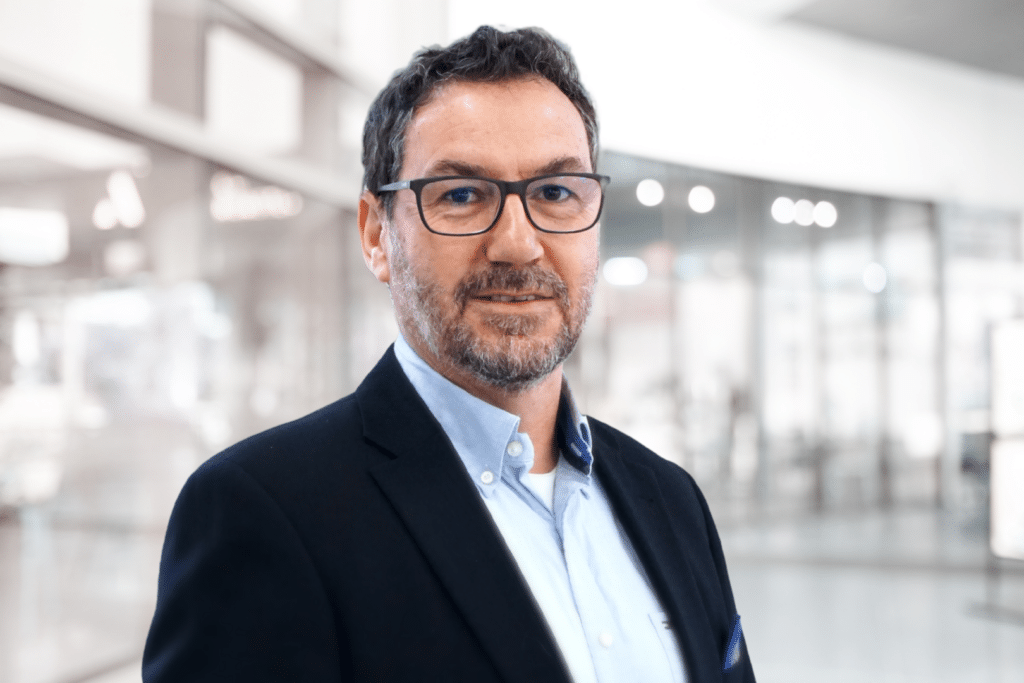
Ihr Experte bei Fragen
- Sven Friedemann
- Technischer Vertrieb
- Tel. +49 3731 37736 - 31
Was ist Entgraten?
Polieren und Entgraten durch gezielte, elektrochemische Metallauflösung.
Die Formgebung von Metallbauteilen erfolgt in der Regel nicht geometrisch perfekt, sondern hinterlässt nach Fertigungsschritten wie dem Drehen. Fräsen, Bohren, Stanzen, Laserschneiden und Wasserstrahlschneiden kleine, überstehende Metallreste an den Fertigungskanten – sogenannte Grate. Diese sind in der Regel scharfkantig, und stellen für Maschinenbediener und Nutzer eine unzumutbare Verletzungsgefahr dar. Zudem können sie Montageprozesse des Bauteils sabotieren und sich im Betrieb ablösen, was je nach Einsatzgebiet erhöhten Verschleiß bis zu fatalen Gesundheitsschäden zur Folge haben kann. Deshalb müssen Grate prozesssicher entfernt werden. In der Regel erfolgt das direkt im Anschluss an den formgebenden Fertigungsschritt.
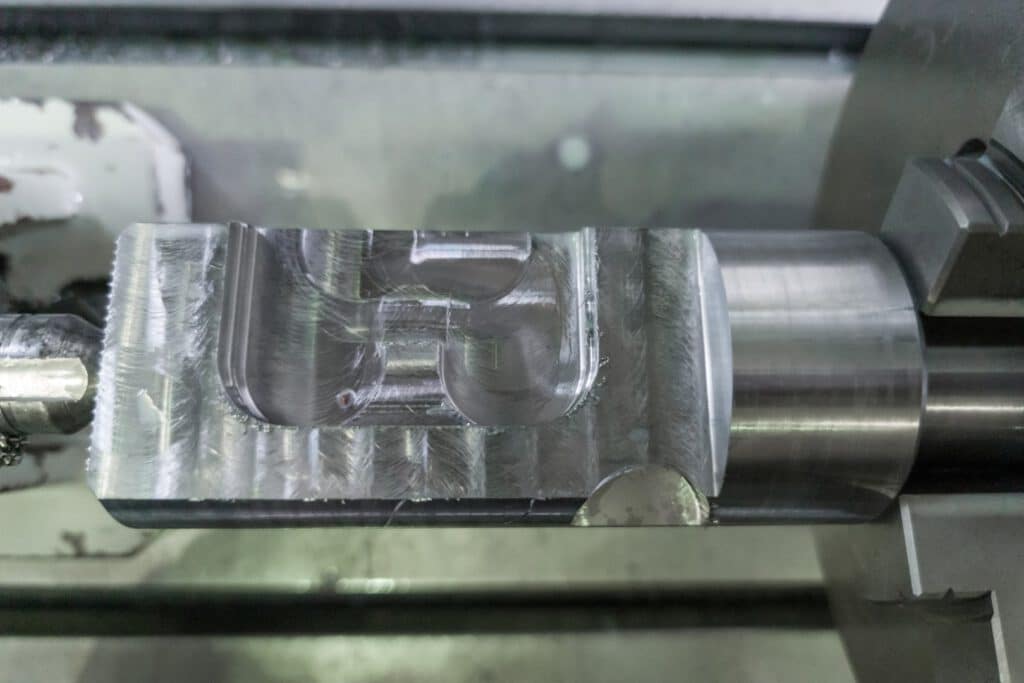
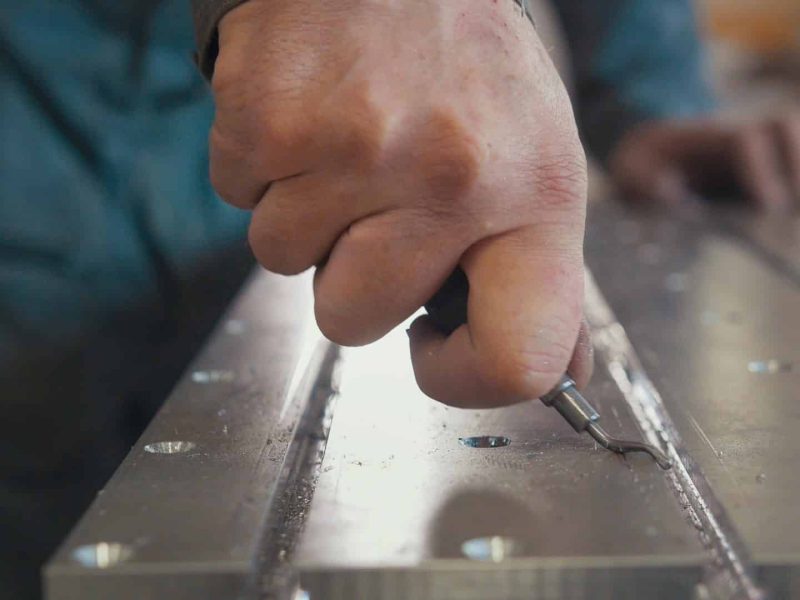
Bedeutung des Entgratens
Das Entgraten ist branchenübergreifend ein entscheidender Schritt in der Fertigungskette.
Gratfreiheit ist in der Regel keine Frage von ästethischer oder technischer Differenzierung, sondern schlichtweg eine Grundanforderung an ein sicheres und funktionales Bauteil. Insofern ist das Entgraten von Metallbauteilen praktisch unabhängig von Industrie und Anwendung ein unerlässlicher Schritt. Aufbauend auf ersten, manuellen Verfahren in diesem Bereich hat sich ein breites Portfolio an Technologien entwickelt, die unterschiedliche Stärken und Grenzen aufweisen. Je nach Anforderungen an Größe, Werkstoff, Taktzeiten, Kantengeometrie etc. ergibt sich eine optimale Wahl.
Anwendungsgebiete für das Entgraten
In vielen Branchen und Anwendungsgebieten ist das Entgraten von Metall von entscheidender Bedeutung.
Durch das Entgraten von Metallkomponenten und -bauteilen wird die Funktionalität in Montage und Betrieb sichergestellt. Zudem verlängert eine prozesssichere Gratentfernung auch die Lebensdauer von Maschinen.
Gratfreie Kanten ohne Verrundung sind für die Qualität von Werkzeugkonturen sowie der damit hergestellten Produkte essentiell.
Hier ist Ziel der Bearbeitung oft die Minimierung von Verletzungsgefahren und die Ermöglichung einer präzisen Montage einzelner Bauteile.
Das Entgraten von Metall, ist insbesondere bei Fluidführungen und Karosseriekomponenten aus Stahl und Aluminiumlegierungen üblich, um scharfe Kanten zu entfernen. Dies stellt nicht nur erfolgreiche Montageprozesse sicher, sondern verhindert auch das spätere Ablösen der Grate als Fremdkörper.
Das Entgraten – von verschiedenen medizinischen Geräten und Instrumenten bis hin zu Implantaten – ist eine entscheidende Voraussetzung für den sicheren Einsatz.
Das Entgraten sorgt für die Sicherstellung der reibungslosen Funktion von metallischen Bauteilen in Flugzeugen und Raumfahrzeugen. Aber auch die Einhaltung von Sicherheitsstandards ist hier von wichtiger Bedeutung.
Entgraten in der Medizintechnik
Gratfreie und runde Kanten für sichere Medizinkomponenten
Inbesondere in sensiblen Bereichen muss auf eine prozesssichere Entgratung besonderer Wert gelegt werden. Bauteile in der Medizintechnik, z. B. aus den klassischen Edelstählen 1.4404 (316L) und 1.4542 (17-4PH), weisen nach dem Fräsen und Laserschneiden Mikrograte auf. Die Anforderung an den Prozess ist nicht nur deren zuverlässige Entfernung, sondern oft auch eine Verrundung der Kanten. So werden z. B. Montageprozesse erleichtert, oder das Abreißen von Fäden verhindert.
Technologien für das Entgraten
Die Welt der Entgrattechnologien für Metalle ist extrem vielseitig.
Zwischen bewährt und hochinnovativ – für das Entgraten von Metall stehen verschiedene Verfahren, Ansätze und Technologien zur Verfügung. Die gängigsten stellen wir Ihnen im Folgenden vor.
Wenn Sie für das prozesssichere Entgraten eine nachhaltigere Lösung suchen, mit großen Werkstücken arbeiten oder eine hohe Flexibilität benötigen, bieten wir Ihnen mit unserem Plasmaentgraten einen innovativen Ansatz, der die Grenzen zahlreicher Technologien aushebelt und in diversen Anwendungen neue Maßstäbe setzt.
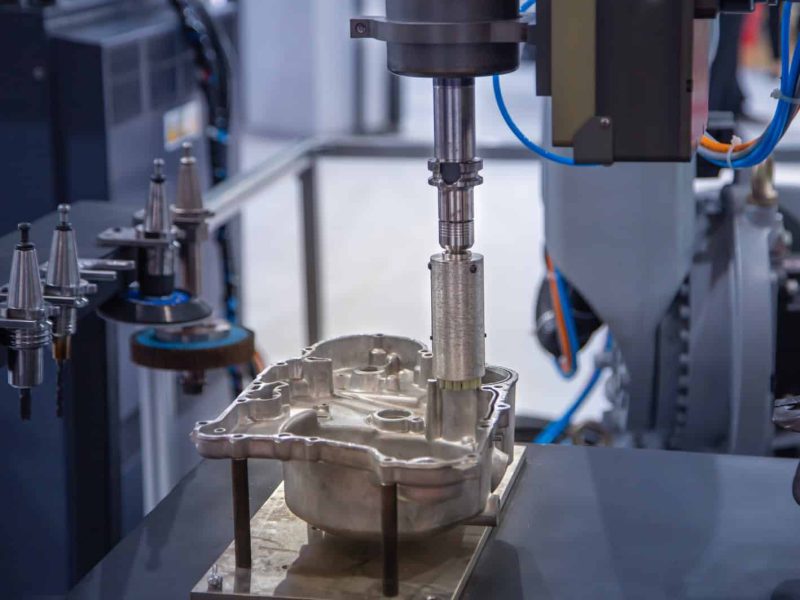
- Manuelles Entgraten
- Maschinelles Entgraten
- Thermisches Entgraten
- Chemisches Entgraten
- Gleitschleifen
- Elektrochemisches Entgraten
- Ultraschall-Entgraten
- Abrasive Strahltechnologien
- Kryogenes Entgraten
Beim manuellen Entgraten werden Grate und scharfe Kanten manuell mit Werkzeugen wie Feilen, Schleifpapier oder Handwerkzeugen entfernt. Diese Methode ist häufig bei kleinen Produktionschargen oder feinmechanischen Bauteilen im Einsatz. Stellen, die für maschinelle Verfahren schwer zugänglich sind, können durch manuelles Entgraten präzise bearbeitet werden.
Die Stärke des manuellen Entgratens liegt in seiner Flexibilität und der Möglichkeit, individuelle Teile präzise zu bearbeiten. Auch erfordert es im Vergleich zu anderen Verfahren eine geringere Anfangsinvestition. Handwerkzeuge sind bereits ab etwa 10 EUR im Handel erhältlich – ein Bruchteil des Investitionsvolumens für eine automatisierte Anlage. Die Kontrolle, die der Bediener über den Entgratungsprozess hat, ermöglicht eine gezielte Bearbeitung von spezifischen Bereichen.
Jedoch ist das manuelle Entgraten zeit- und arbeitsintensiv, was es bei großen Serien schnell unwirtschaftlich macht. Zudem ist es stark von den manuellen Fähigkeiten und Erfahrungen des Bedieners abhängig. Die Konsistenz der Ergebnisse kann und wird deshalb variieren. Auch wenn das manuelle Entgraten noch in vielen Bereichen der Industrie eingesetzt wird, ist ein immer stärker werdender Automatisierungsdruck spürbar. Grund hierfür sind nicht nur notwendige Kosteneinsparungen im Entgraten, sondern steigende Qualitätsanforderungen der Kunden und der Mangel an Fachkräften für solche repetitiven, manuellen Tätigkeiten.
Maschinelles Entgraten nutzt Fräs- oder Bürstwerkzeuge, um Grate von Werkstücken zu entfernen und Kanten zu verrunden. Diese Methode ist für Serienproduktionen, große Bauteile und die präzise Entgratung von Metallteilen ideal. Die Maschinen ermöglichen eine hohe Präzision, Geschwindigkeit und Wiederholbarkeit im Entgratungsprozess, was sie insbesondere für schnellgetaktete Prozesse in der Automobilindustrie unerlässlich macht.
Die Stärke maschineller Verfahren liegt in ihrer Fähigkeit, große Stückzahlen an Teilen effizient zu bearbeiten. Die Prozessautomatisierung sorgt für eine konstante Qualität der entgrateten Teile. Diese Methode ist anpassungsfähig für verschiedene Materialien und ermöglicht eine präzise Kontrolle über den Entgratungsprozess. Sollen an CNC-Teilen exakte Kantenradien eingestellt werden, führt zudem oft kein Werk am maschinellen Entgraten vorbei. Hierfür gibt es jedoch auch innovative und flexible Alternativen, siehe Plasmaentgraten.
Allerdings erfordert maschinelles Entgraten eine Investition in spezialisierte Maschinen, was anfängliche Kosten verursacht. Zudem erfordert der Verschleiß von Werkzeugen eine regelmäßige Wartung. Insbesondere an komplexen Geometrien ist die Zugänglichkeit für diese Werkzeuge zudem einschränkt, sodass kein Entgraten möglich ist.
Das thermische Entgraten ist ein Verfahren, das der thermisch-chemischen Gratentfernung basiert. In einem geschlossenen Reaktionsraum wird ein Gemisch aus Brenngas und Sauerstoff gezündet. Die entstehende Wärmeenergie dissipiert innerhalb von weniger als einer Sekunde, verbrennt bzw. verdampft dabei aber die von bauteilkanten abstehenden Grate. Diese Methode ist besonders effektiv bei harten Materialien und kann Grate beseitigen, die durch Bearbeitungsprozesse wie Fräsen oder Schleifen entstanden sind.
Einsatzbereiche für thermisches Entgraten umfassen häufig Teile, bei denen eine hohe Genauigkeit und Präzision erforderlich sind. Es eignet sich gut für industrielle Anwendungen, in denen Grate an schwer zugänglichen Stellen oder in komplexen Geometrien im Bauteilinneren entfernt werden müssen. Stärken dieses Verfahrens liegen in seiner Fähigkeit, Grate an Metallbauteilen effizient und präzise zu beseitigen. Dank der gezielten Verbrennung sind selbst Innenbohrungen mit großen Aspektverhältnis kein Problem. Zudem weist das Thermische Entgraten, insbesondere in der Serie, eine der geringsten Stückkosten für die Bearbeitung auf.
Nachteile des thermischen Entgratens ergeben sich aus der Wirkung des Brenngases – Oxidationen, Verfärbungen und andere ungewünschte Effekte sind zu erwarten. Diese müssen insbesondere bei Eisenwerkstoffen in einem Nachprozess korrigiert werden. Auch ist es möglicherweise nicht für empfindliche Materialien geeignet, da diese durch die Wärmebehandlung beschädigt werden könnten. Eine Verrundung von Kanten durch Thermisches Entgraten ist nicht möglich, was seine Anwendung insbesondere in der Medizintechnik einschränkt. Zudem wird die maximale Bauteilgröße durch die Größe der Brennkammer begrenzt.
Chemisches Entgraten ist ein Verfahren, das chemische Lösungen zur Gratentfernung nutzt, die den zu bearbeitenden Werkstoff auflösen. Dabei wird eine auf die Bearbeitungsaufgabe abgestimmte Chemie eingesetzt. Diese greift das Bauteil an allen, auch schwer erreichbaren Stellen an, jedoch bevorzugt an hervorstehenden Graten. Diese werden schneller, aber nicht ausschließlich aufgelöst. Insofern kommt es je nach Einwirkzeit im Bad auch zu einer mehr oder weniger ausgeprägten Bearbeitung der Oberfläche durch das Reduzieren von Rauheiten. Das Verfahren eignet sich besonders gut für komplexe Geometrien und schwer zugängliche Bereiche, da die Lösung in der Lage ist, alle Grate problemlos zu erreichen. Industriell wird es meist für unlegierte Stähle als Schüttgut eingesetzt, da hier eine besonders effiziente Entgratwirkung möglich ist.
Eine Stärke des chemischen Entgratens liegt in seiner Fähigkeit, gleichmäßig und schonend zu entgraten. Insbesondere bei feinen Graten kann so eine prozesssichere Entfernung bei kurzen Taktzeiten sichergestellt werden. Es ist jedoch wichtig, äußerste Vorsicht bei der Handhabung der chemischen Lösungen zu walten, da diese in der Regel stark umwelt- und gesundheitsgefährdend sind.
Entgraten durch Gleitschleifen nutzt Schleifkörper und Wasser, um Grate von Metallbauteilen zu entfernen. Dieses Verfahren ist besonders geeignet für wenig komplexe Teile ohne schwer zugängliche Bereiche. Hier ermöglicht es eine gleichmäßige Bearbeitung und trägt in der regel zur gleichzeitigen Verbesserung der Oberflächenqualität bei.
Die Stärken des Gleitschleifens liegen in seiner Anpassungsfähigkeit an verschiedene Formen und Materialien sowie der Fähigkeit, diverse Geometrien gleichzeitig zu entgraten. Da die Anlagentechnik etabliert und günstig ist, können Prozesse oft mit geringen Investitions- und Betriebskosten aufgebaut werden.
Die maximale Bauteilgröße ist beim Gleitschleifen anlagenseitig begrenzt. Es ist jedoch zeitaufwändiger als einige andere Methoden und kann bei ungünstiger Handhabung zu Oberflächenveränderungen führen.
Das elektrochemische Entgraten ist ein präzises Verfahren, das auf elektrochemischen Reaktionen basiert, um Grate von Metallbauteilen zu entfernen. Das Bauteil, die Gegenelektrode und ein Elektrolyt bilden eine elektrochemische Zelle, in der unter einer Gleichspannung herausstehende Oberflächenmerkmale wie Rauheitsspitzen und Grate gezielt abgetragen werden. Im Grunde ist es das Gegenteil von galvanischer Beschichtung. Das abgetragene Metall sammelt sich im Elektrolyten an, und muss hieraus entfernt werden. Das elektrochemische Entgraten wird häufig eingesetzt, um Grate an schwer zugänglichen Stellen oder in komplexen Geometrien zu beseitigen.
Die Stärken dieses Verfahrens liegen in seiner Präzision und Unabhängigkeit von der Härte des Werkstoffs. So können auch gehärtete Metallbauteile, die mechanisch eine Herausforderung darstellen würden, problemlos bearbeitet werden. Die schnelle Entgratwirkung ermöglicht eine der schnellsten Taktzeiten unter den Entgratverfahren.
Zentraler Nachteil ist zunächst die geometriespezifische Werkzeugkathode. Diese erfordert entsprechende Erstinvestitionen für jede neue Bauteilform. Zudem braucht es beim elektrochemischen Entgraten eine spezialisierte Ausrüstung und Expertise sowie eine genaue Kenntnis der Materialverträglichkeit, da nicht alle Metalle für das Verfahren geeignet sind. Zudem ist die Technologie nur für Metallteile mit feinen und sehr konstanten Graten geeignet, da größere den Arbeitsspalt zur Kathode überragen und zu einem Kurzschluss führen können.
Ultraschall-Entgraten wirkt nicht durch die Ultraschallwellen selbst, sondern macht sich die Trägheit von Wasser zunutze. Das Bauteil befindet sich bei diesem Verfahren in einem Prozesswasserbecken, begleitet von einer gratnah geführten Sonotrode – einem Ultraschallschwinger. Diese schwingt so schnell vor und zurück, dass das umgebende Medium nicht hinterher kommt und in sogenannten Kavitationsblasen implodiert. Hierdurch wird ein hochbeschleunigter Wasserstrahl ausgestoßen, der Grate entsprechend prozesssicher abreißt.
Das Ultraschallentgraten wirkt punktuell, und kann Grate schonend von Metallbauteilen entfernen. Die Methode eignet sich gut für kleinere Teile und ermöglicht präzise Entgratung. Das eingesetzte Prozessmedium ist arbeitsschutzseitig als unkritisch zu bewerten – in der Regel handelt es sich um Wasser mit Calcium-Carbonat als Zusatz.
Seine Grenze findet das Ultraschallentgraten in größeren Bauteile oder bei massiven Gratbildungen, insbesondere ausgeprägten Gratwurzeln. Zudem sind nicht alle Werkstoffe bearbeitbar.
Bei abrasiven Strahltechnologien werden abrasive Partikel verwendet, um Grate von Metallbauteilen zu entfernen. Diese werden mithilfe von Druckluft oder Rotation beschleunigt und treffen mit entsprechend hoher kinetischer Energie auf das Bauteil auf.
Dieses Verfahren erweist sich als effektiv, und kann uafgrund der lokalisierten Wirkung im Aufprallbereich gezielt gesteuert werden, wenngleich aufgrund der Abpraller nicht exakt in einem abgegrenzten Bereich. Für das Partikelstrahlen ist auch eine Handführung möglich.
Die Methode kann für weichere Materialien weniger geeignet sein. Dabei ist eine präzise Steuerung wichtig, um Schäden am Bauteil zu vermeiden. Zudem erfordert diese Technologie oft eine genaue Überwachung des Prozesses, z. B. des Verschleißes des Strahlmediums, welcher das Ergebnis signifikant beeinflusst.
Beim kryogenen Entgraten werden Teile bei extrem niedrigen Temperaturen behandelt, um Grate sicher zu entfernen. Mithilfe von flüssigem Stickstoff werden die Grate auf Temperaturen unterhalb von -100°C heruntergekühlt, was sie fest und spröde macht. Anschließend wird das Metallbauteil mit Granulat, in der regel Kunststoff, beschossen, was die Grate abschlägt.
Das kryogene Entgraten wirkt schonend und verzugsfrei, wobei keine negative Beeinflussung der Oberfläche zu verzeichnen ist.
Dieses Verfahren ist effektiv, jedoch können die Ausrüstungskosten hoch sein und die Handhabung extrem niedriger Temperaturen stellt eine Herausforderung dar. Es eignet sich gut für eine Vielzahl an Metallen, weist aber auch Grenzen auf. So ist z. B. das kryogene Entgraten von Stählen nicht möglich.
Sie wollen die Grenzen der Ihnen bekannten Technologien gezielt umgehen?
Die Alternative: Plasmaentgraten
Effizienteres Entgraten durch Plasmaphysik und Elektrochemie in einer Technnologie.
Sauber und gratfrei in einem Prozessschritt? Für das gezielte Entgraten und Verrunden von Kanten an Metallbauteilen setzen immer mehr Unternehmen auf die einzigartige Plasmaentgrat-Technologie von plasmotion.
Plasmaentgraten bietet mit seinem einzigartigen Wirkprinzip – der Überlagerung von elektrochemischem und plasmaphysikalischem Abtrag – einen hocheffiziente Alternative zu mechanischen oder chemischen Technologien. Innerhalb weniger Sekunden können Grate entfernt und Kanten gezielt verrundet werden, und das ohne nennenswerte thermische oder mechanische Einflüsse.
Wir beraten Sie selbstverständlich gern zum Potential des Plasmaentgratens für Ihre Anwendung. Sprechen Sie unsere Experten an!
Als einziger Lösungsanbieter verfügt plasmotion über das volle Spektrum der plasmaelektrolytischen Oberflächenveredlung: klassisch im Elektrolytbad, und selektiv mit dem Elektrolytstrahl. Sie benötigen beim Entgraten von Metallbauteilen Unterstützung, oder stehen gar vor einer schwierigen Herausforderung? Gerne schauen wir uns gemeinsam Ihr Anliegen und Ihre Situation an, um eine passende Lösung zu finden. Mit unserem weltweit einzigartigen Technologieportfolio werden wir (fast) jeder spezifischen Oberflächenherausforderung gerecht.
Plasmaentgraten
Sie legen Wert auf Qualität, Effizienz und Zuverlässigkeit? Dann könnte unser Plasmaentgraten auch für Ihre Anwendung das Richtige sein. Beim Eintauchen Ihres Werkstücks in unsere speziellen Elektrolyte verkochen diese unter Anlegen einer Gleichspannung auf der Oberfläche, und bilden einen konturtreuen Dampffilm aus. Hier kommt es zum einzigartigen plasma-elektrolytischen Abtrag von Graten und Mikrorauheiten, bei gleichzeitiger Bauteilreinigung.
JETPEP: Jet-Plasmaentgraten
Mit JETPEP ist plasmotion die Innovation gelungen: der plasma-elektrolytische Abtrag wird in einem Strahl erreicht und kann so flächengenau wirken. Diese Technologie kann nicht nur zur Oberflächenveredlung durch Polieren eingesetzt werden, sondern auch zum gezielten Entgraten, insbesondere von komplexen Bauteilen. Prozesssichere Gratentfernung und selektive Verrundung sind so auch vollautomatisierbar möglich – ob mit Roboter, Achskinematik oder Multidüsencluster.
Leistungen von plasmotion
Plasmaentgraten ist in Ihre Fertigung nahtlos integrierbar.
Unser einzigartiges Wirkprinzip können Sie nicht nur im Rahmen der Lohnfertigung nutzen. Mit unseren kundenspezifischen Anlagenlösungen haben Sie Zugriff auf eine Technologie, die nicht nur mehr Effizienz, sondern auch mehr Nachhaltigkeit durch den Einsatz wässriger Salzlösungen erlaubt. Ersetzen Sie staubige, unflexible und manuelle Prozesse durch das Plasmaentgraten – wir beraten Sie gern!
Ihre nächsten Schritte
Machen Sie Ihre Fertigung zukunftssicher – mit Plasmaentgrat-Lösungen von plasmotion.
Ihre Herausforderung – unsere Lösung. Ihr direkter Weg zum individuellen Angebot.
Lassen Sie uns über Ihre spezifischen Anliegen sprechen.
Gerne überzeugen wir Sie ganz konkret anhand Ihrer Bauteile von den Stärken und Möglichkeiten unserer Technologien. Der erste Schritt ist dabei eine Bemusterung. Sprechen Sie uns einfach an.
Sie haben Fragen zu unseren Technologien und Anwendungen?
Ihre Werkstoffe und Oberflächen haben spezielle Anforderungen? Sie sind sich unsicher, ob Plasmaentgraten das Richtige für Ihr Produkt ist? Sie wollen wissen, wie plasmotion Sie als Lösungsanbieter voranbringen kann? Ich beantworte Ihre Fragen gerne persönlich.
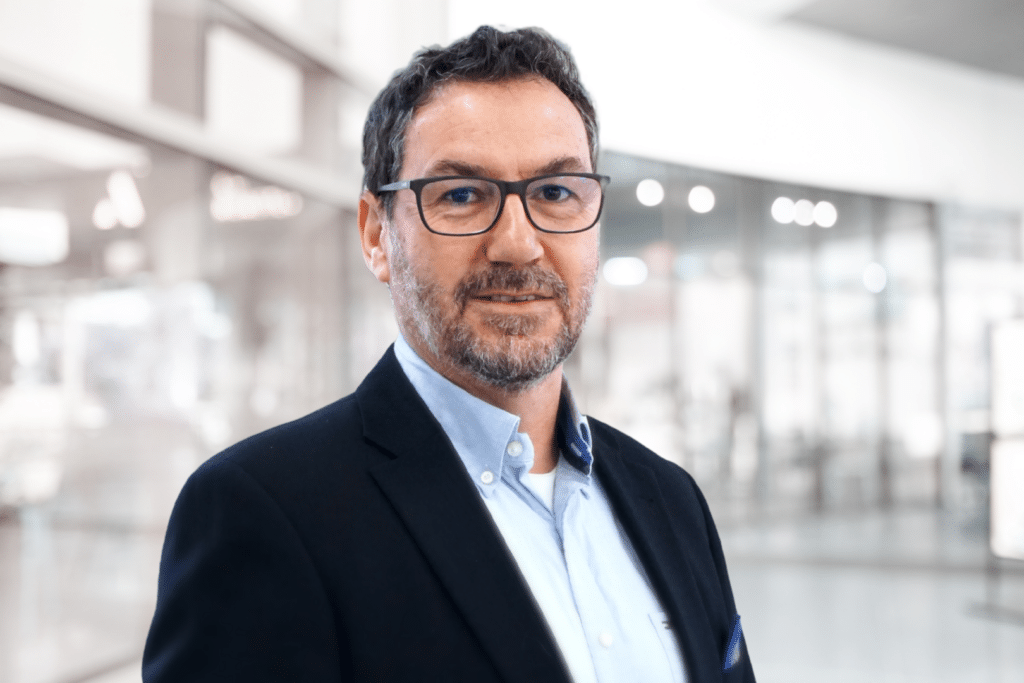
Ihr Experte bei Fragen
- Sven Friedemann
- Technischer Vertrieb
- Tel. +49 3731 37736 – 31
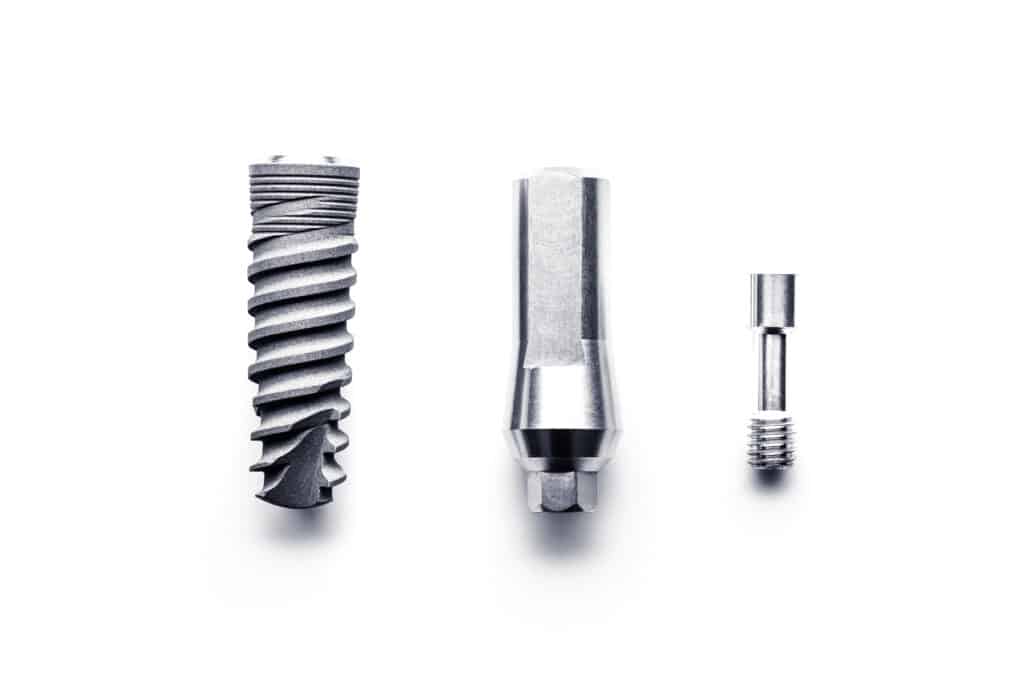