High-gloss polishing
High-gloss polishing at a glance
plasmotion brings your surfaces to a high gloss efficiently and sustainably.
plasmotion is your contact and expert when it comes to automated high-gloss polishing. With the help of our modern and innovative plasma polishing technologies, we achieve a gloss level on stainless steel workpieces in particular that significantly exceeds that of electropolishing. These results are achieved with process times on a minute scale and environmentally friendly salt solutions as electrolytes. We are therefore setting new standards in this area too.
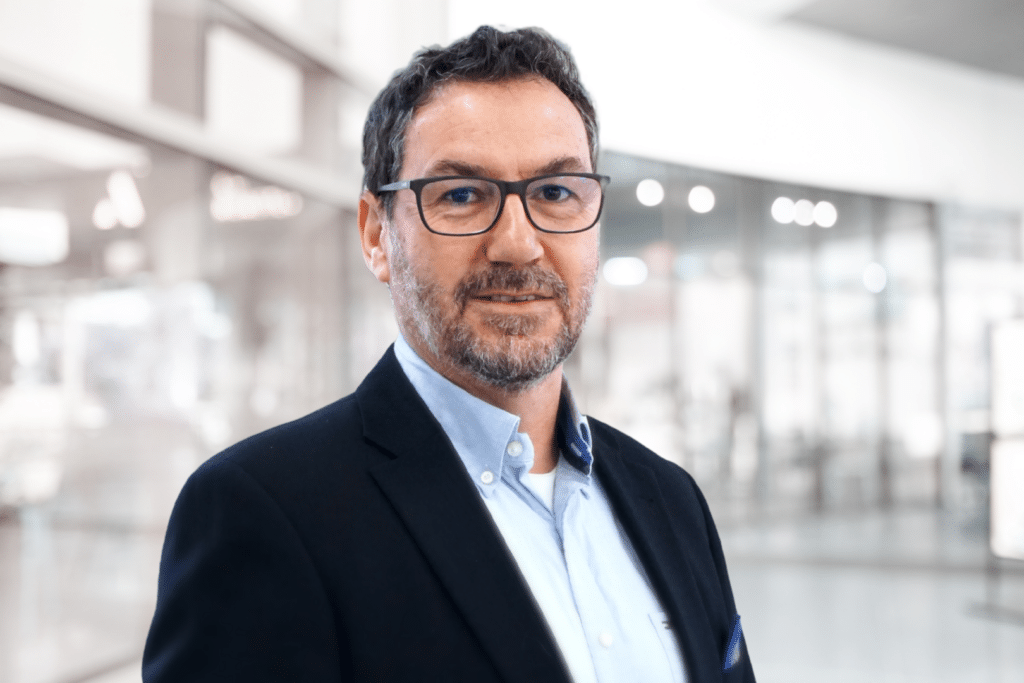
Your expert for questions
- Sven Friedemann
- Technical sales
- Phone +49 3731 37736 - 31
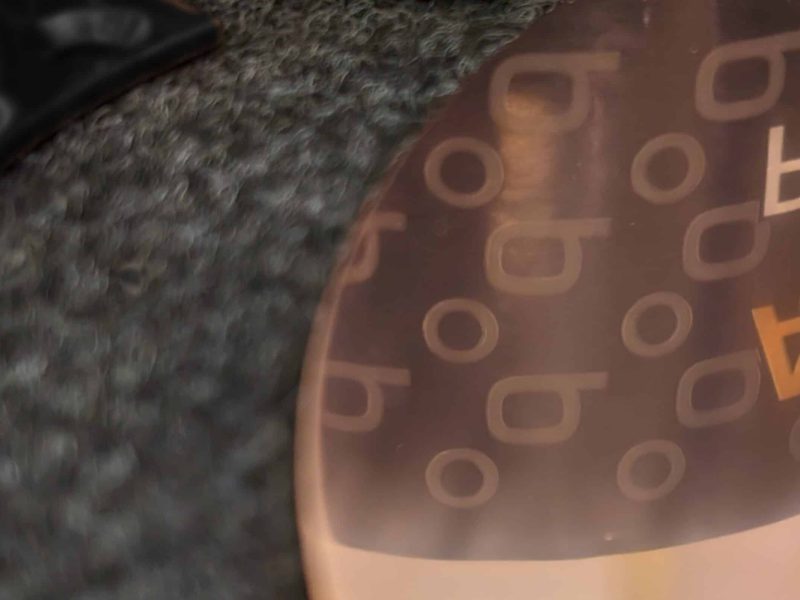
What is mirror polishing?
High-gloss polishing - for flawlessly smooth surfaces
Whether visual or functional - our high-gloss polishing processes have already successfully proven their strengths in various industries. For example, when it comes to polishing machine components that are exposed to high loads. In the following, we take a closer look at high-gloss polishing and name individual areas of application.
At the same time, we will be presenting our plasma polishing and JETPEP technologies, which you can use to take your applications and production to the next level.
Where is a high-gloss polish used?
High-gloss polishing is omnipresent.
The technology is suitable for polishing the surface of medical devices and instruments. This makes cleaning easier and minimizes the risk of germs forming or adhering.
High-gloss polishing of surfaces optimizes the aerodynamic properties. At the same time, the aesthetics are improved.
Various components such as exhaust pipes, body parts or wheel rims are polished to a high gloss. This also includes the polishing of decorative elements and the polishing of paintwork.
In the manufacture of precision mechanics, the surface is polished to a high gloss in order to optimize its functionality. This is the case, for example, with optical instruments and precision tools.
In the manufacture of electronic devices, surfaces and housings are polished to a high gloss in order to refine them.
Smooth surfaces ensure that hygiene standards are met. But product safety also plays a decisive role.
By the way: High-gloss polishing of metal is not only used in the industrial sector. It is also common in the craft and private sectors to bring a surface to a high gloss using a polishing machine and polishing agents (polishing paste, sandpaper). For example, when polishing plastic, polishing wood, polishing steel, polishing plastic and polishing clear lacquer.
TECHNOLOGIES FOR HIGH-GLOSS POLISHING
Various processes are available for high-gloss polishing.
This method is most commonly used to polish a surface. Abrasive media such as abrasive pastes and/or sandpaper are used here. A distinction must also be made between manual and machine polishing, depending on whether automated tools are used.
This is a combination of chemical reactions and mechanical grinding to polish a surface on a microscopic level. This process is mainly used in the electronics and semiconductor industries.
This technology is often used to polish a metal surface. The workpiece to be treated is immersed in an electrolyte solution. By applying an electrical voltage, metal ions are removed from the surface, preferably at roughness peaks and edges. This levels the surface.
More information on electropolishing.
Ultrasonic waves are used to move abrasives across a surface - ideal for complex and hard-to-reach areas.
In mass finishing, the surface is leveled using small grinding wheels in which the workpiece is moved in a similar way to a washing machine. A soapy water solution ensures the correct contact parameters and the removal of the ground metal.
Do you want to bypass the limits of the technologies you are familiar with?
The alternative: plasma polishing
More efficient mirror polishing through plasma physics and electrochemistry.
Do you want to polish your components to a high gloss and attach great importance to the best results? Then our plasma polishing could be just the right technology - as an alternative to conventional and perhaps already unsuccessfully tested high-gloss polishing processes.
When plasma polishing from plasmotion is a targeted combination of electrochemistry and plasma physics in a single process. We are setting a new standard when it comes to high-gloss polishing and metal finishing. Thanks to the unique active principle, we achieve roughnesses of up to Ra 0.02 µm, even if this means a reduction of 90% - 95%.
This means that the shape of components is almost completely retained - even with complex geometries. At the same time, the surface is cleaned, polished, deburred and sterilized in a single operation - in just 20 to 200 seconds using environmentally friendly electrolytes.
Materials
Which materials is plasma polishing suitable for? Despite or perhaps because of the material-specific electrolytes from plasmotion, the range of materials that can be processed now covers practically all alloy groups - from stainless and tool steels, titanium, copper and Inconel to aluminum and special alloys. Not all of them are suitable for mirror polishing. Our experts will be happy to answer any questions you may have.
These points speak in favor of high-gloss polishing by plasma polishing:
- Highly efficient: Plasma polishing is a highly efficient process for high-gloss polishing, as it cleans, polishes, deburrs and sterilizes the surface in a single work step. This also eliminates the need for pre-treatments such as cleaning.
- Sustainable: We use special, proprietary electrolytes. These are aqueous salt solutions with active components. They are 100% harmless according to REACH, recyclable and create safe working conditions.
- Gentle: The component temperature is limited to 100 °C in the machining area. This makes it possible to process delicate and heat-treated or surface-hardened parts - without any loss of quality!
- Reliable: Even when high-gloss polishing large quantities, plasma polishing ensures consistent results.
The alternative to electropolishing
Plasma polishing is qualitative, efficient & reliable.
Do you value quality, efficiency and reliability when machining your components and tools? Then our process plasma polishing is just right for you. The alternative to electropolishing removes even the smallest burrs and micro-roughness from the surface structure - in a matter of seconds, gently and reliably.
With our innovative process, you can quickly achieve the desired surface finish in just one step. Which alloy would you like to process? We will find a suitable solution!
How plasma polishing works
Perfected with plasmotion.
During plasma polishing, the workpiece is processed in an electrolyte bath. Special electrolytes in the form of aqueous salt solutions are used. The electrolytes evaporate on the surface at a DC voltage of between 200 and 400 volts, depending on the material, and form a reactive vapor plasma shell.
This now flows around the workpiece surface and adapts to the respective contours. The electrochemical and plasma-physical processes remove burrs and micro-roughness. At the same time, impurities are removed. This has the advantage that no degreasing or cleaning is required before high-gloss polishing.
JETPEP - jet plasma polishing
JETPEP - the solution for precise surface finishing or large workpieces
With JETPEP is an innovative process from plasmotion. With this modern technology, the plasma-electrolytic removal takes place in a jet instead of a bath, and is therefore precise and flexible in terms of surface area.
With JETPEP not only the high-gloss polishing possible at a high level. At the same time deburring complex components in a targeted manner. Various settings (roughness, gloss) are possible depending on the processing requirements. The process is also fully automated - optionally with robots, axis kinematics or multi-nozzle clusters.
Do you have any questions? Please contact us.
Your challenge - our solution. Your direct route to a customized offer.
Let's talk about your specific concerns.
We would be happy to convince you of the strengths and possibilities of our technologies based on your components. The first step is a sampling. Simply get in touch with us.
Do you have questions about our technologies and applications?
Do your materials and surfaces have special requirements? Are you unsure whether plasma polishing is right for your product? Would you like to know how plasmotion can help you as a solution provider? I will be happy to answer your questions personally.
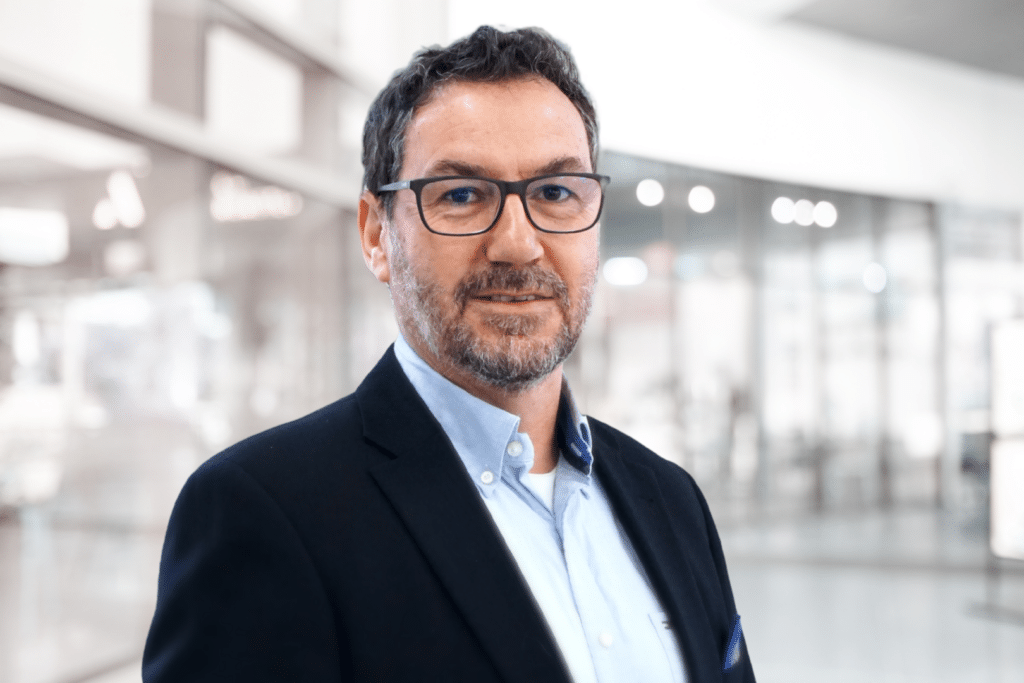
Your expert for questions
- Sven Friedemann
- Technical sales
- Phone +49 3731 37736 - 31
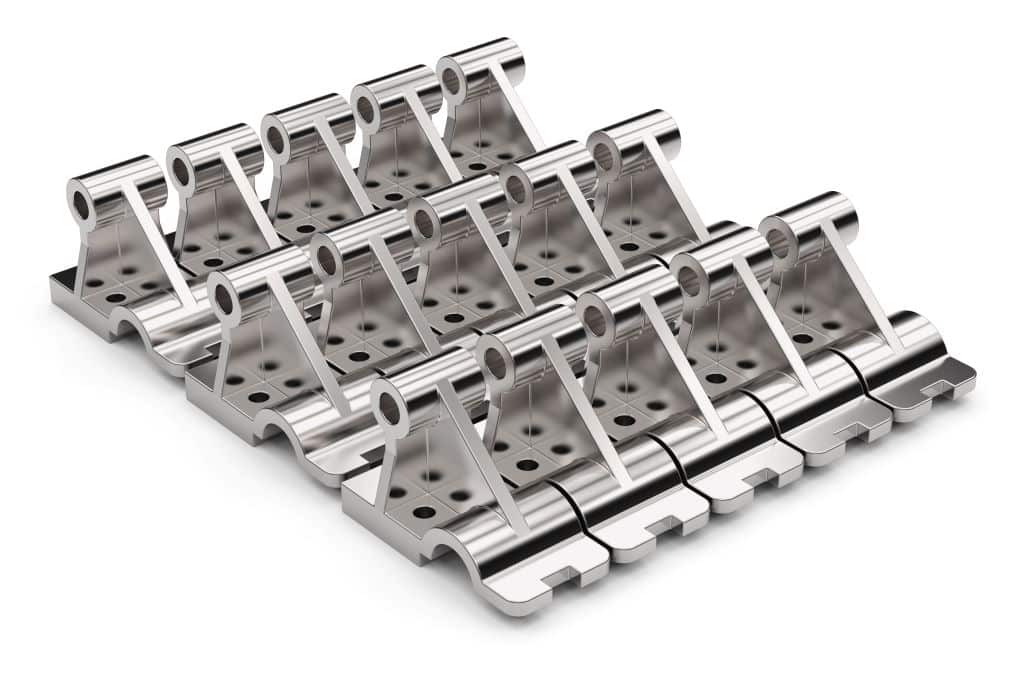